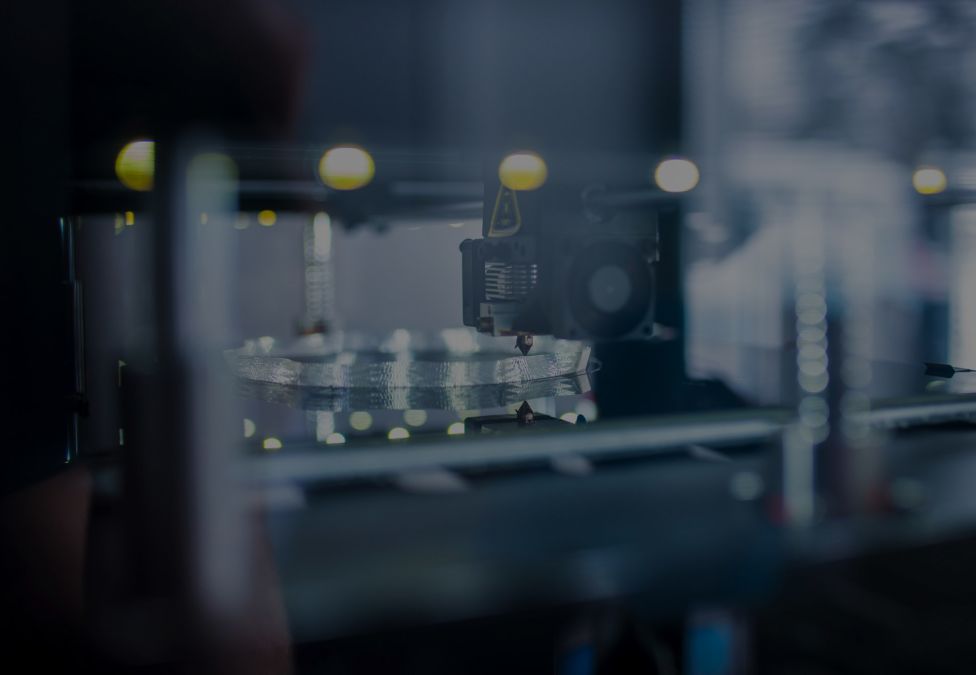
One of my earliest observations about the global pandemic was how local it was. The response to COVID-19 had to happen everywhere, and not just in places that already had readily available production lines of in-demand supplies—everything from PPE to medical equipment or hand sanitizer.
As we addressed supply shortages, working collectively across industry, academia, and government, the future of manufacturing really started to come into focus. And here’s what it looked like: glocal.
The term “glocal” reflects an interesting shift happening in manufacturing sparked largely in response to COVID-19. The pandemic showed us how essential global innovation is, forging new networks and collaborations around the critical supplies and vaccines that the world needed. But as supply chains were disrupted, we also saw how important it is to be able to establish local production capabilities that increase resiliency against future disruptions.
Glocalization empowers manufacturers to have the best of both worlds—access to the most innovative ideas and the means to produce them closer to market demand. And it’s enabled by digital transformation.
Here’s an example. Not long after the pandemic started, ventilators were desperately needed by health-care providers but in short supply around the world. So, the medical device company Medtronic asked Siemens if we could digitally capture the design of its ventilator, creating what we call a digital twin of the physical product. The idea was, if we can make the plans, specifications, and instructions for the ventilator digitally available to other manufacturers, they could license the intellectual property and begin producing it. We could accelerate speed-to-need like never before.
Fast forward to conversations we’re having now around the shortage of semiconductors, a critical component to how we’ll build smarter, more resilient, and more sustainable infrastructure. I was honored to take part in a recent White House roundtable with other industry leaders, where I shared our perspective on how applying digital technologies can help optimize the domestic production of semiconductors over both the short and long term. Designing, producing, and packaging these chips is a complex process. But by using software to digitally represent the complete product lifecycle, creating a digital thread, manufacturers can have greater security, transparency, and trusted traceability from start to finish.
We’re already working with the Food and Drug Administration to explore the possibilities in this space. In a new showcase, we’ll demonstrate how digital threads can improve the design process of medical devices, streamline workflows, and enable more efficient regulatory reviews so life-saving products can get to patients as quickly and as safely as possible.
Now it’s clear that investments in manufacturing are investments in crisis preparedness, national security, and global leadership.
And it’s worth noting that our capacity to transform manufacturing goes well beyond modeling and simulation. With additive manufacturing, or 3D printing, we’re no longer limited by the ways things have been done in the past, when a design could be optimized by software but its physical creation still relied on traditional production processes. The technology we have today enables manufacturers to build anything they can see on a computer screen and do it faster and with less waste.
What’s underscored in these examples is the connection between the modernization of manufacturing and a region’s economic competitiveness. Before the pandemic, the legacy production lines and systems in factories might have seemed like an industry issue. Now it’s clear that investments in manufacturing are investments in crisis preparedness, national security, and global leadership.
Here are two final points I’ll make on the advantages of a “glocal” mindset. The first is that a manufacturing world where we’re more efficient with resources promises to be a huge step forward in our efforts for sustainability. With today’s technologies, we can drive competitive and profitable economies of mass customization instead of mass production. We can do more with less—saving costs and the planet at the same time.
Last, and most importantly, is the opportunity these tools give us to elevate the capability and productivity of every person. It’s less about finding the lowest cost of labor and more about having the toolbox of technologies that can help create well-paying jobs and pathways to success for people, anywhere and everywhere.
Looking back on the past year and a half, there’s no shortage of examples of change sparked by COVID-19, in both our personal and professional lives. But in manufacturing, those changes have challenged us to think “glocally” and truly reimagine what’s possible. Let’s use these lessons to grow stronger and more resilient for years to come.